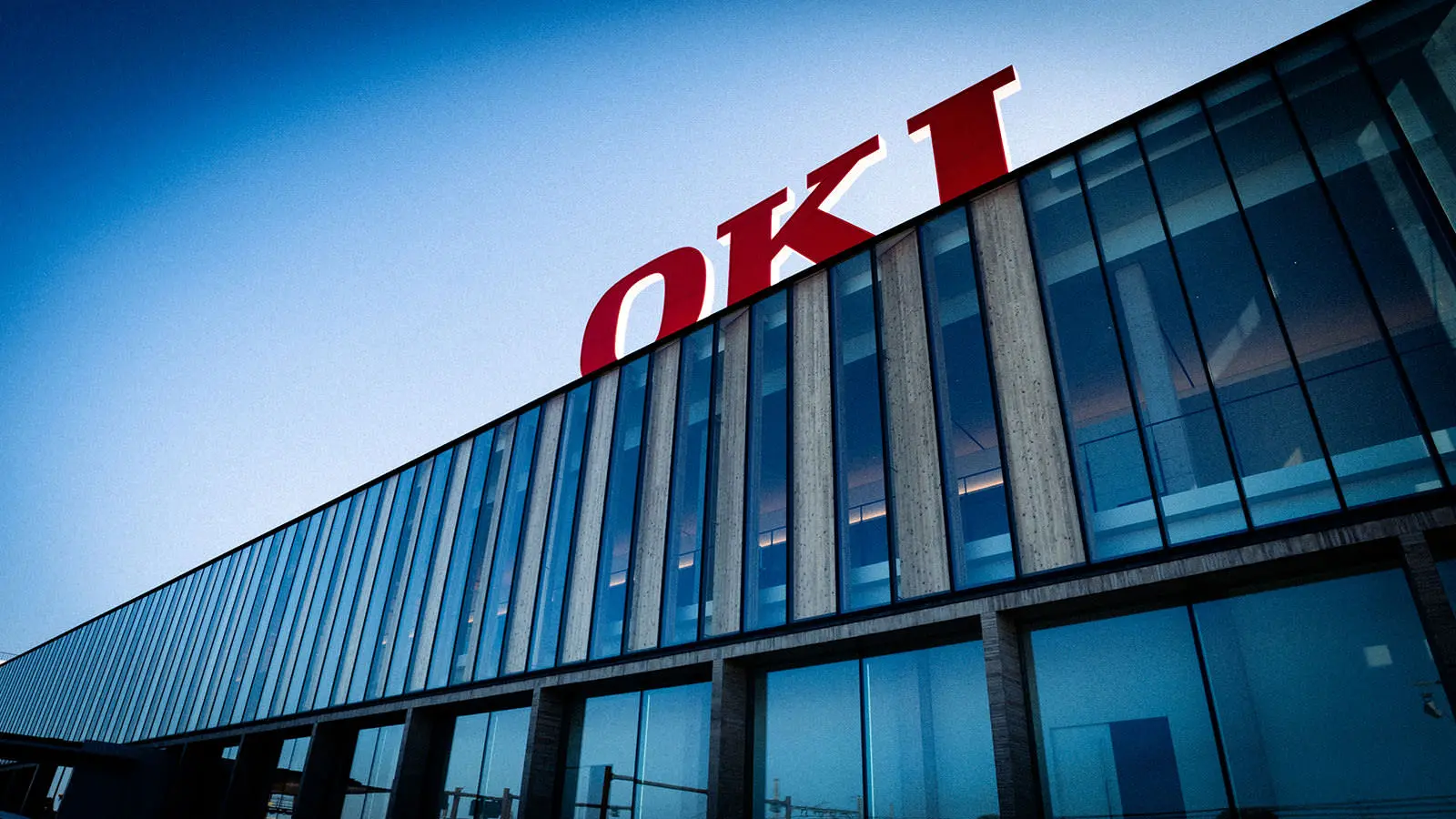
The Changing Manufacturing Industry and the Future of the Communications Networks that Support It--Exploring the Production Site Today at OKI's Honjo Plant
XGMF ODAIBA IX Core Report
The "XGMF-ODAIBA IX Core Fusion of Cutting-edge Industrial Technology and Cutting-edge Communication Technology (IX) Workshop (Vol. 6)" was held at Oki Electric Industry's flagship factory, the new Honjo Plant (Saitama Prefecture). From the workshop held in the H1 building, production sites...
2025/07/18
Posted on 2025/07/18
The "XGMF-ODAIBA IX Core Fusion of Cutting-edge Industrial Technology and Cutting-edge Communication Technology (IX) Workshop (Vol. 6)" was held at the new Honjo Plant (Saitama Prefecture), the flagship factory of Oki Electric Industry. The "OKI Honjo Plant H1 Building," which welcomed the workshop group, is a production base completed in April 2022 with maximum consideration for the environment and local community. The workshop was held at the H1 Building, and the participants learned about DX and EMS projects at the production site, as well as the current status of wireless communication at the factory. The following is a report on the workshop held in the H1 building.
Modernizing the plant while incorporating local traditions
Oki Electric Industry's (OKI) Honjo factory has a history of more than 60 years. Within it is a new factory with the latest equipment, called the H1 building. Takashi Matsubara, plant manager of the Honjo Plant, Production and Procurement Management Division, said, "Honjo is located in the northernmost part of Saitama Prefecture, with Gunma Prefecture right next door. The city has a population of about 80,000 between Kumagaya and Takasaki, and is a land of cold winters and hot summers. It is said that the production of vegetables such as leeks and cucumbers thrives here, and as the 10th post town in the old Nakasendo period, it was the most prosperous on the Nakasendo route," he explains about Honjo's location. A little to the west is the Tomioka Silk Mill, and there are many buildings devised for sericulture in Honjo. Following such traditional innovations for industrial production, the H1 building incorporates a system for air circulation and was constructed to reduce energy consumption as much as possible to approach zero energy consumption.
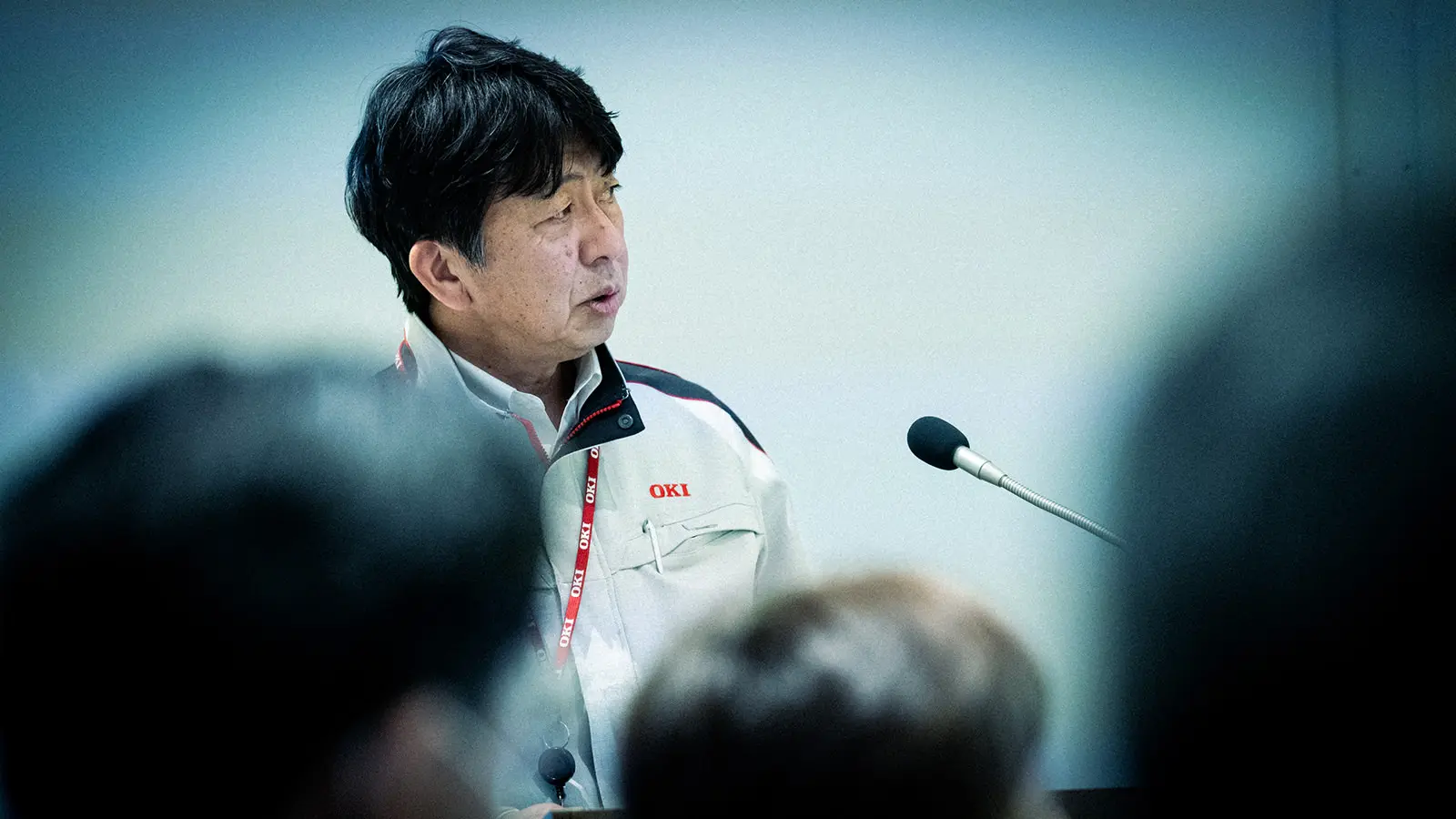
Takashi Matsubara (Plant Manager, Honjo Plant, Production & Procurement Management Division)
The Honjo Plant H1 Building features a "Smart Factory," "Virtual One Factory," "ZEF (Net Zero Energy Factory) as Japan's first production facility," and "Provision of comprehensive manufacturing services.
As a smart factory, named "Honjo Smart," it is promoting visualization, automation, and AI utilization. In the visualization area, production data is collected and visualized, and operations are recorded as video data to speed up the process of identifying problems and implementing countermeasures and improvements. In the area of human-robot collaboration, automation is being promoted in the form of sharing the work in which both parties excel, and in the area of AI utilization, for example, the company is working to recognize the skeletal movements of workers and determine whether they are performing abnormal movements.
OKI, which has been engaged in manufacturing for more than 100 years, aims to become a virtual one-factory company by virtually connecting multiple factories to create a complementary manufacturing resource system as if they were a single factory. One practical example of this is the portability between factories. The product lines manufactured at the Numazu Plant have been transferred to the Honjo Plant for production. It was not easy," recalls Matsubara, "because the structure and culture differ from one factory to another.
And the H1 building will be the first large-scale production facility in Japan to receive ZEB certification. The ZEB certification was awarded to the building based on the adoption of a seismic isolation structure that does not sway in the event of an earthquake, the abundant use of wood from Chichibu in Saitama Prefecture to reduce CO2 emissions, and a design that reduces energy consumption for air conditioning by circulating air. In the future, we want to go from carbon zero to carbon negative," Matsubara said of the H1 building's future.
EMS business to accelerate integrated manufacturing services
The phrase "comprehensive manufacturing services," which is one of the features of the Honjo factory, indicates that it is a base for providing the Electronics Manufacturing Service (EMS) business, which was launched in 2002 in response to the contraction of the telephone equipment and switching equipment business. Hiroshi Nishimura, Senior Executive Officer and General Manager of the EMS Business Division, said, "Our contract manufacturing business, which started from scratch, has grown to the point where it will reach 100 billion yen in size by FY2028. We are focusing on the semiconductor field, metrology, information and telecommunications, and industrial equipment, as well as medical and aerospace areas," he said.
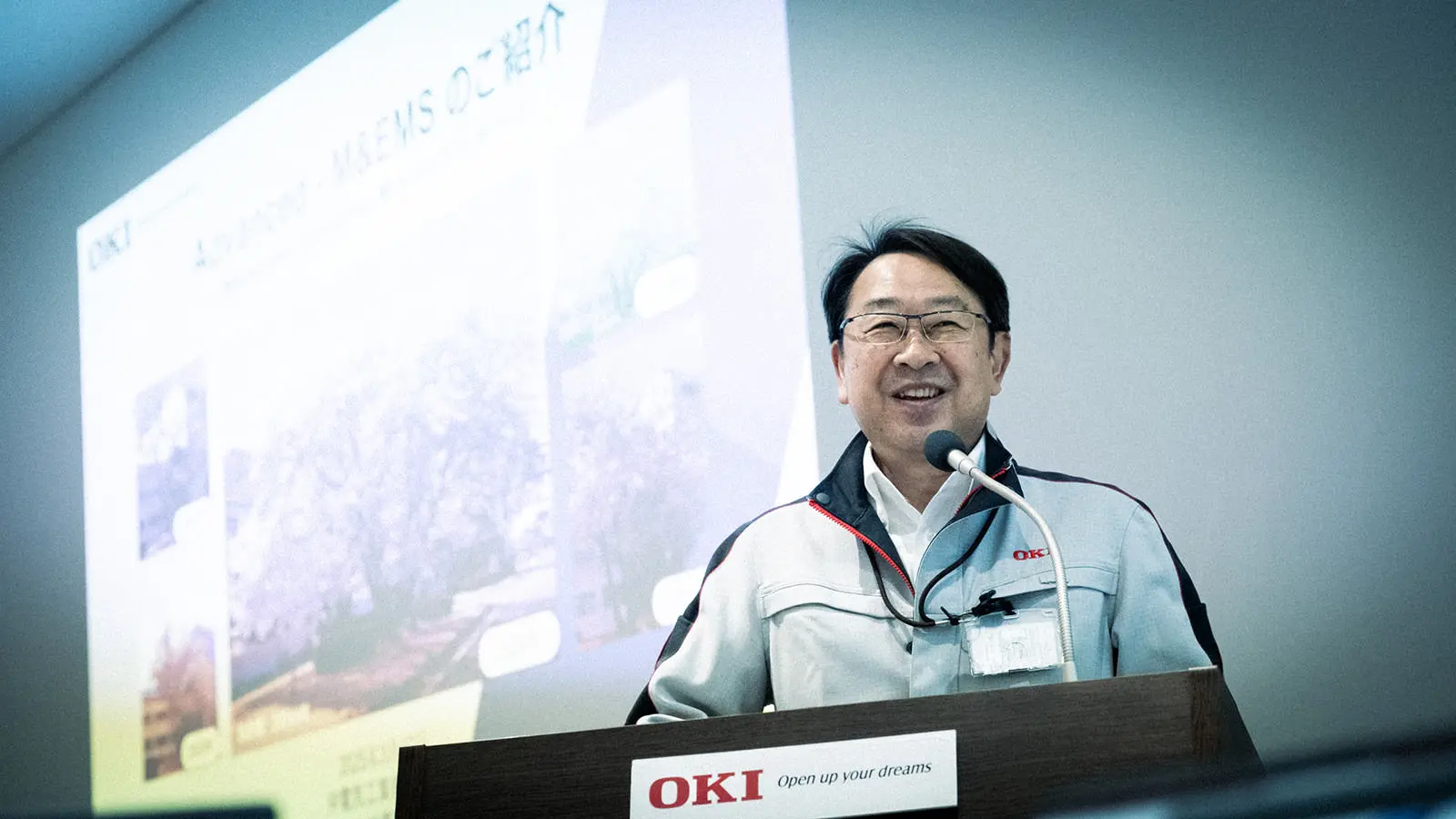
Mr. Hiroshi Nishimura (General Manager / Senior Executive Officer, EMS Division)
OKI's EMS is not simply a production outsourcing business, although it is contracted production. OKI's style is to handle all processes involved in production, including development, evaluation, certification, and logistics. Many people think of Taiwan's Hon Hai Precision Industry, which is engaged in contracted production of iPhones, as a so-called EMS. However, OKI's EMS does not target mass-produced products. Mr. Nishimura explains, "Mass production is strong in China and other Asian countries, so OKI specializes in high-value-added areas. Aerospace is the most important area of focus, and other areas include medical equipment, advanced infrastructure for information and telecommunications, and measuring equipment," he says.
Typical examples of their business are elevator control units, gas station payment terminals, and printed circuit boards for JAXA's rockets.
In the EMS business, the company is also looking into providing "Out-Out service," which directly links overseas factories to overseas markets. This is because there are calls for overseas production even among domestic companies with overseas markets. We will provide EMS Out-Out services for ATMs, printers, medical equipment, etc. that are manufactured at OKI's operations and sold in Asia and Europe," said Nishimura.
OKI's technological strengths to achieve high quality and reliability
Kurando Maeno, Executive Officer and CTO, General Manager of the Technology Division, says of OKI's technology, which continues to evolve in spite of its history and tradition. OKI's core competence is 'toughness. We provide high performance, high quality, high reliability, and high availability to realize unstoppable and unstoppable social infrastructure. The company has long been known as the OKI of terminals, and the tradition of being good at making products and components with high quality and high reliability is still being carried on there. The company also pursues high quality and high reliability, including systems that highly integrate products and operations that do not stop services.
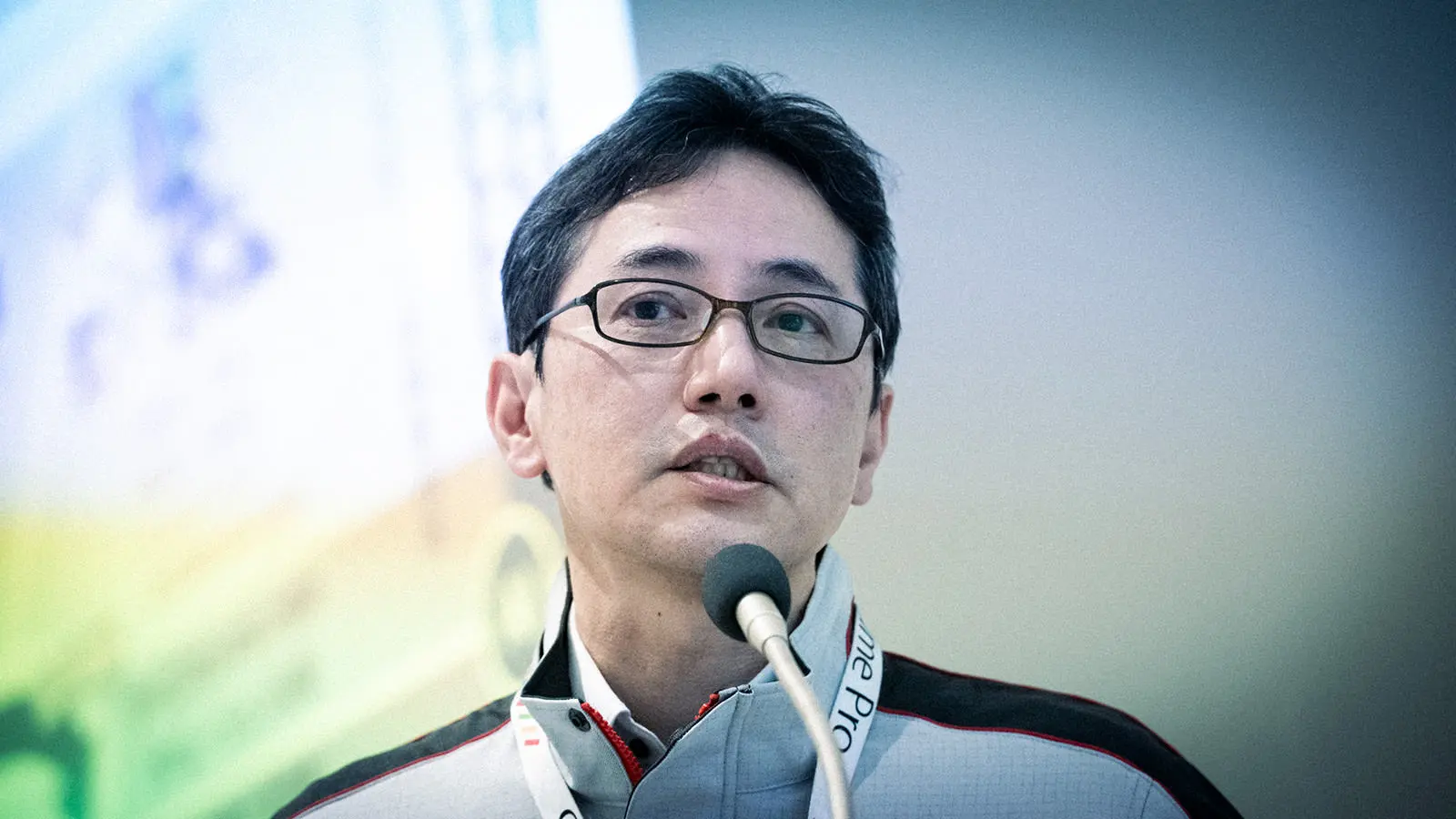
Mr. Kurato Maeno, Executive Officer CTO, General Manager, Technology Division
To improve the quality of operations, edge sophistication and data management will be essential. To promote this efficiently, we are working on an edge platform that realizes the crossover of massive and realistic data processing and AI technology. On top of this, the company intends to provide value to all corners of society through reliable data exchange with mobility and "toughness" communication technologies that support social infrastructure. Mr. Maeno says, "We would like to create new added value by crossing different industries around data.
Another of OKI's strengths is its extensive knowledge of analog as well as digital technologies. Currently, OKI is focusing its R&D efforts on "silicon photonics," the siliconization of optical circuits for communication and sensing applications, "optical fiber acoustic sensors" to understand underwater sound and vibration, "millimeter wave sensing" for application to intelligent road traffic systems, etc., and "vibration, temperature, and strain sensors" that use optical fibers for sensing. Vibration, temperature, and strain sensors" that use optical fiber for sensing.
In addition to these in-house technologies and research, the company opened a startup exploration base in Silicon Valley in May 2024. The company will promote the search for open innovation startups and aim to expand the coverage of technologies that are not limited to its own technologies.
The Challenge of Wireless Factory Networks
As a production base for EMS and other businesses, the Honjo Plant's H1 Building is being converted to a smart factory with the latest equipment. This is an advanced example of the OKI Group's efforts to promote the smart factory concept across the entire plant. Keisuke Yamada, team manager of the Advanced Production Technology Development Department in the Production and Procurement Management Division, which is promoting smart factory conversion, said, "We are automating production processes, introducing and deploying AMR (Autonomous Mover Robot), utilizing production simulators, and introducing process management systems. In addition, we are also working on lead analysis and guidance systems, warehouse management systems, AI work analysis systems, and factory infrastructure monitoring," he says.
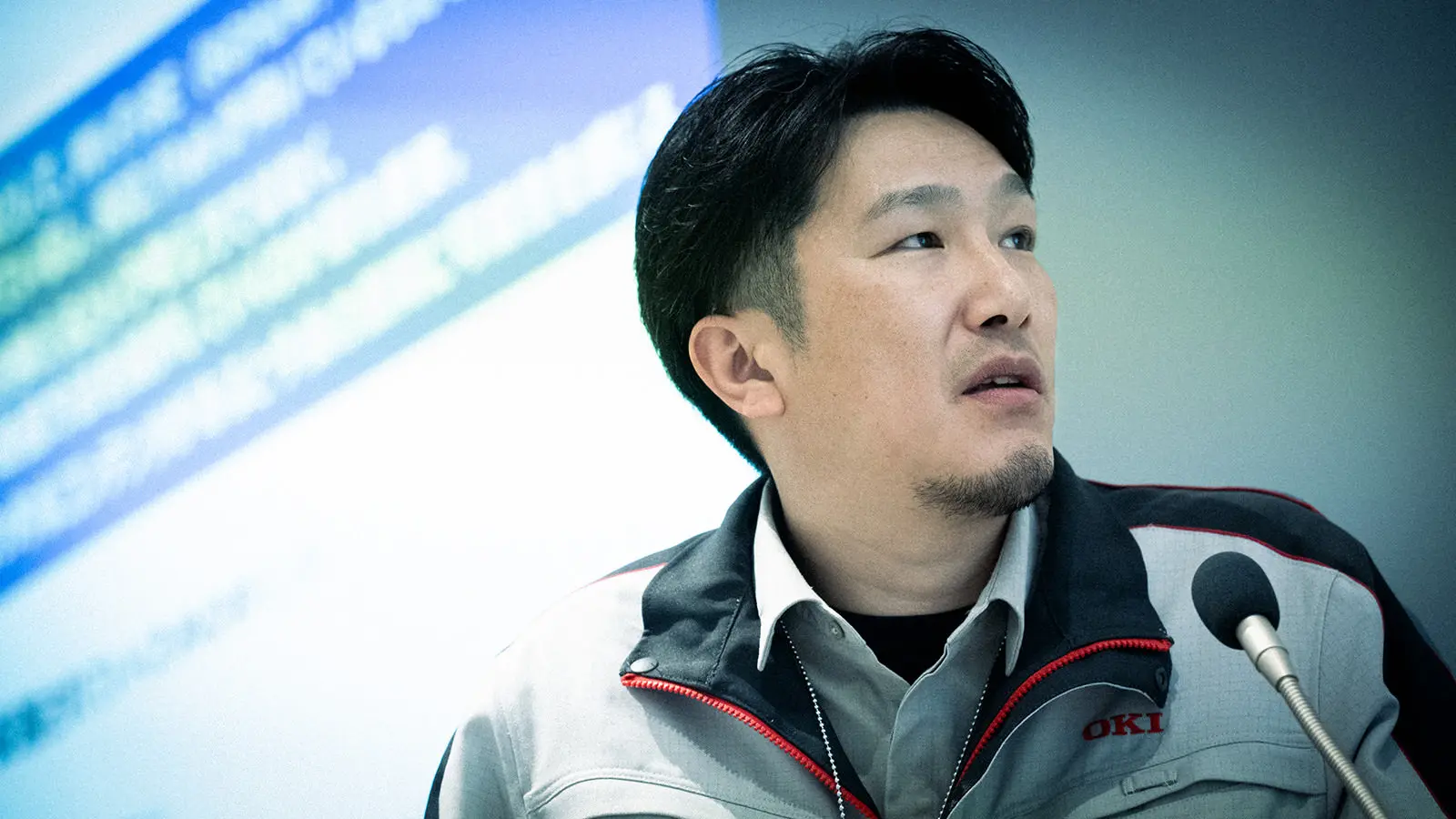
Keisuke Yamada, Team Manager, Advanced Production Technology Development Department, Production and Procurement Management Division
An essential element in these diverse smart factory initiatives is the network. For example, in a process control system, many tablets are deployed in the process to data the start and end of work and to implement initiatives to improve work. We have to use a wired connection for stability, but we are currently using a USB-LAN converter for the wired connection," says Yamada. There are many other devices that require network connectivity, but wireless connectivity is not possible because even the slightest network disconnection can cause problems. Mr. Yamada muses, "Wired connections are a burden when creating new or changing layouts, so uninterrupted wireless is ideal.
Automated transport systems using AMRs also have issues with network connectivity. Currently, AMR is controlled via Wi-Fi connection, but the Wi-Fi sometimes disconnects. They have responded by increasing the number of access points, modifying the program to handle some disconnections, and adopting IEEE 802.11r for high-speed roaming to handle disconnections during handovers. In addition, the H1 building is a two-story structure, and SSID differences when moving from one floor to another were resolved by introducing a separate common SSID exclusively for AMR. When using wireless, many such minor adjustments are necessary. There are also other unforeseen challenges, "It is difficult to completely eliminate the use of stray Wi-Fi, such as pocket Wi-Fi and tethering, which are prohibited by law, and realistically, interference can occur in the 2.4GHz band," he said.
There are plans to use AMR to transport between buildings in the future. At that time, the use of local 5G will also be considered. Even with Wi-Fi, it costs over 10 million yen to maintain a single factory building. There is talk that local 5G is expensive, but recently we have seen the possibility of suppressing initial costs through the provision of a subscription model," says Yamada.
In smart factory infrastructure monitoring, the company hopes to promote optimization of electricity, gas, liquid, boiler, and other usage fees, centralized monitoring, and more efficient inspections. One issue to be considered is whether image processing and inference should be performed at the edge or on the server. If images are sent directly to the server, traffic will increase, but with edge AI, cost will be an issue when the number of devices increases. If we consider local 5G as a network, we feel that we will have more configuration options," said Yamada.
Yamada says that both wired and Wi-Fi networks are available for production sites, and he sees the potential for local 5G. Rather than thinking about replacing everything with local 5G, it would be good if we could take the best of both worlds and use them in the right places. As the barriers to local 5G adoption drop and attractive content emerges, the potential for local 5G deployment at production sites will increase.
In addition to "lower costs for installation and maintenance" and "abundance of client-side compatible devices and lower costs," the key to lowering the barriers to introduction is "the cost of obtaining a license," which is currently too difficult for factories to easily use. Mr. Yamada added, "As a system, we need to be able to use it easily when we want to use it. In addition, we, the users, will have to think about how to devise a system to improve production efficiency by taking advantage of local 5G.
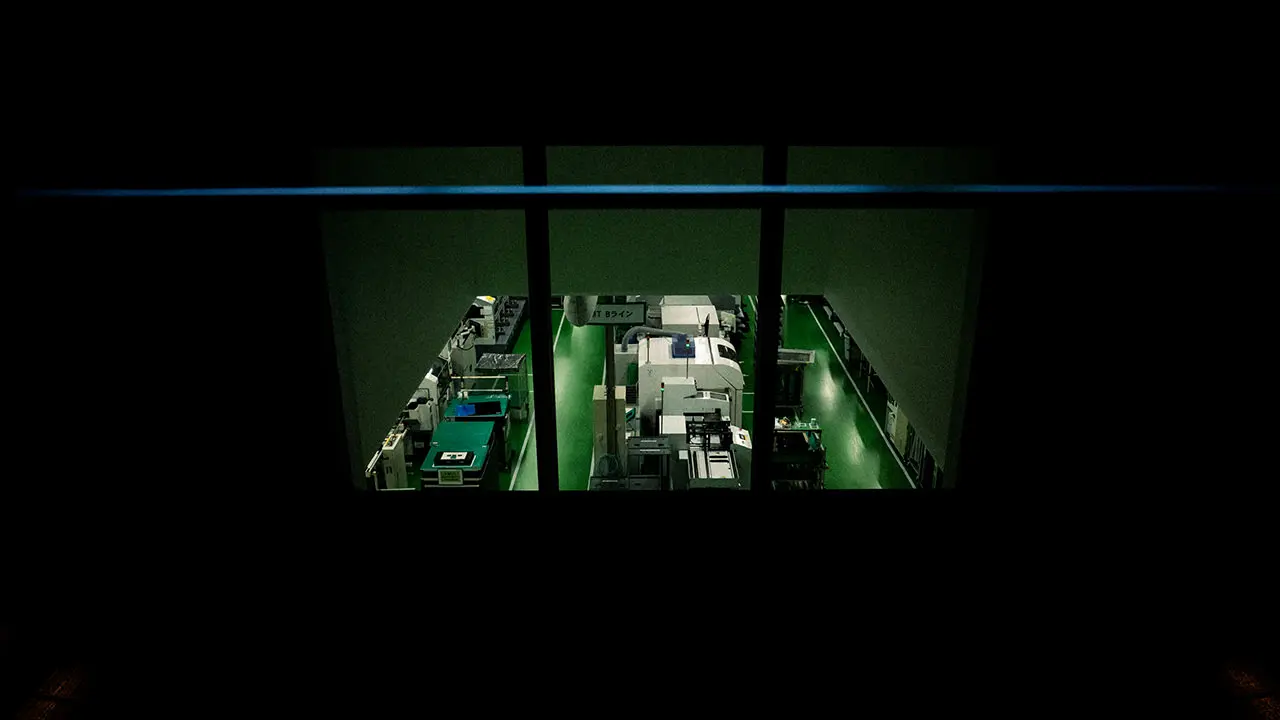
The inside of the factory can be viewed through a window attached to the showroom.
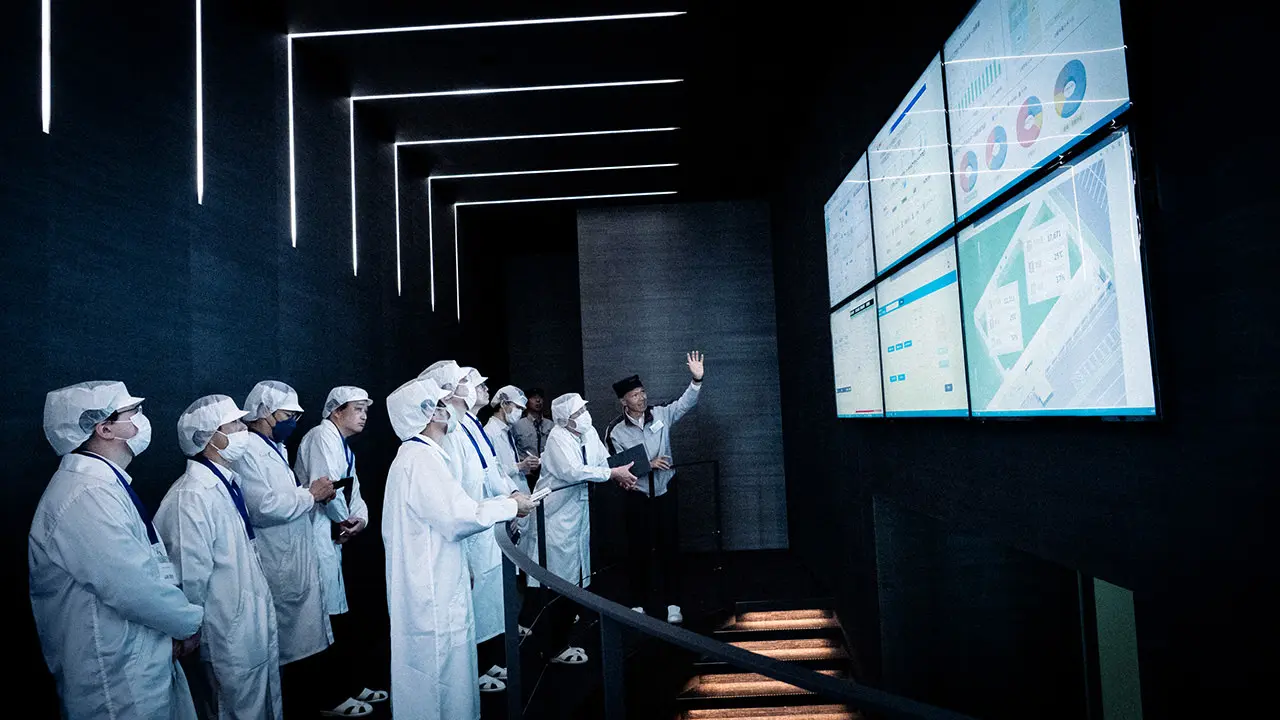
Receive an overall view of the plant
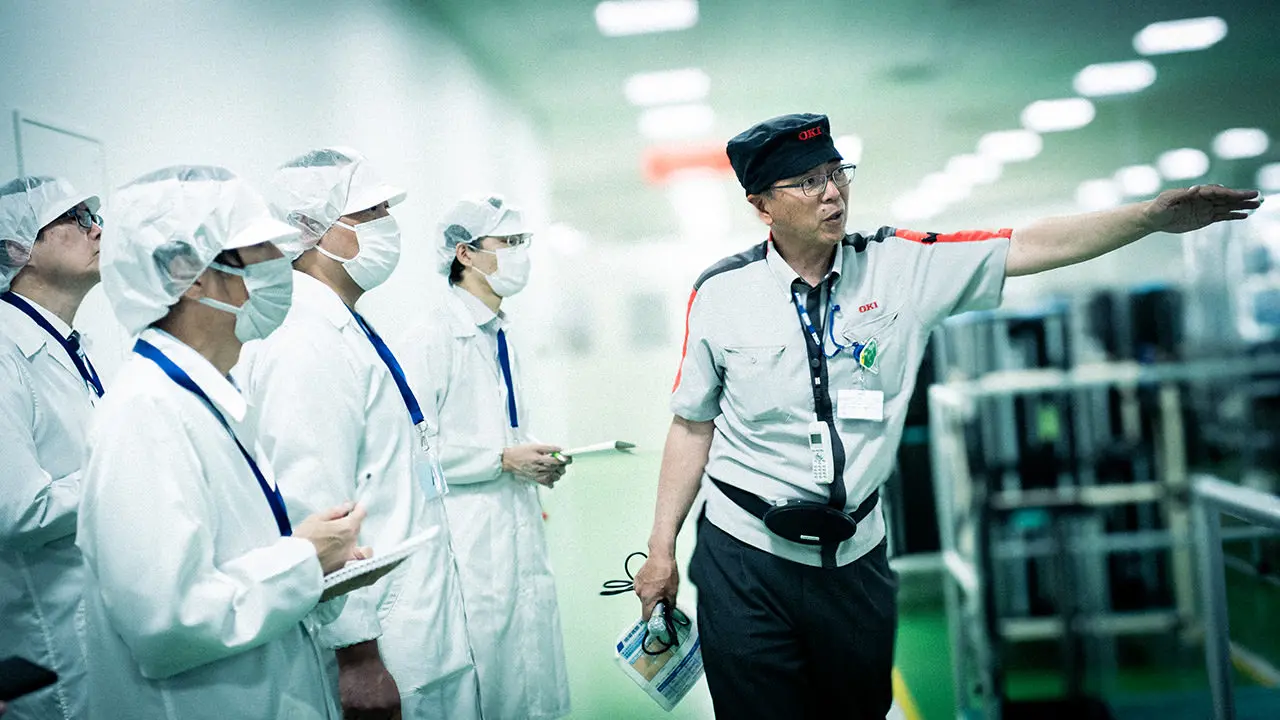
A tour of the factory. The explanation by the engineer in charge is very easy to understand.
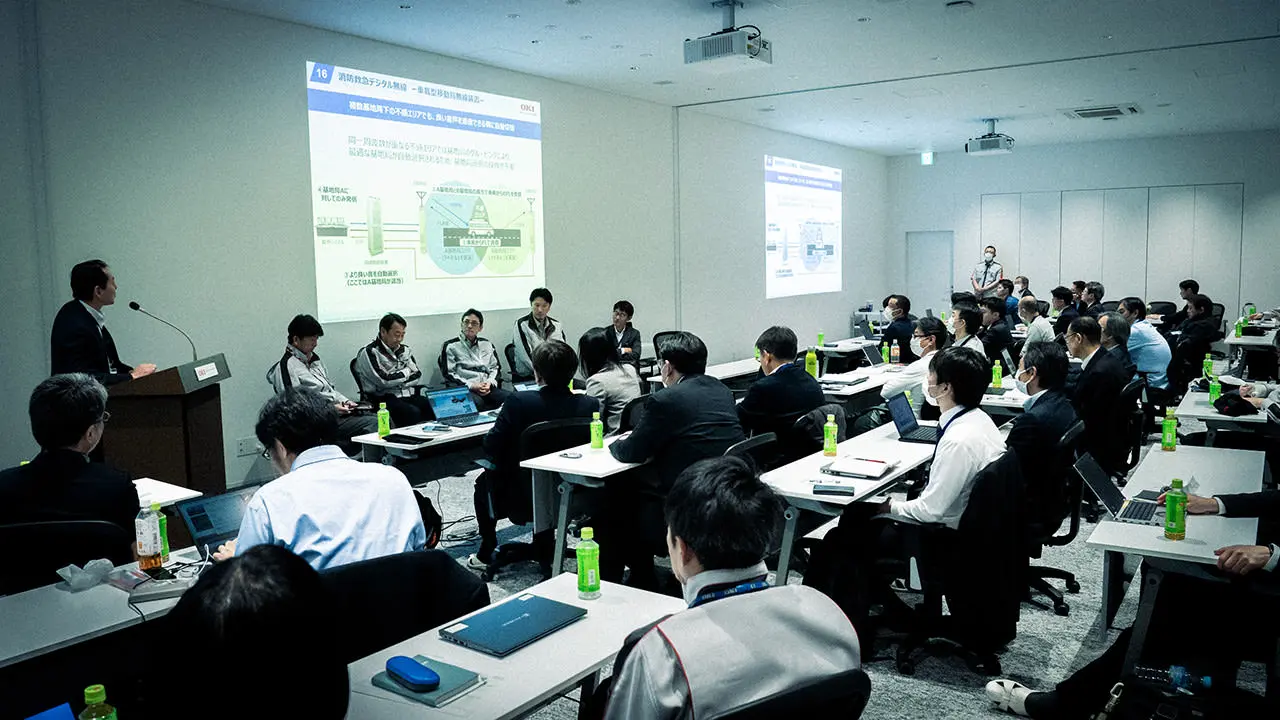
Discussion held after the factory tour
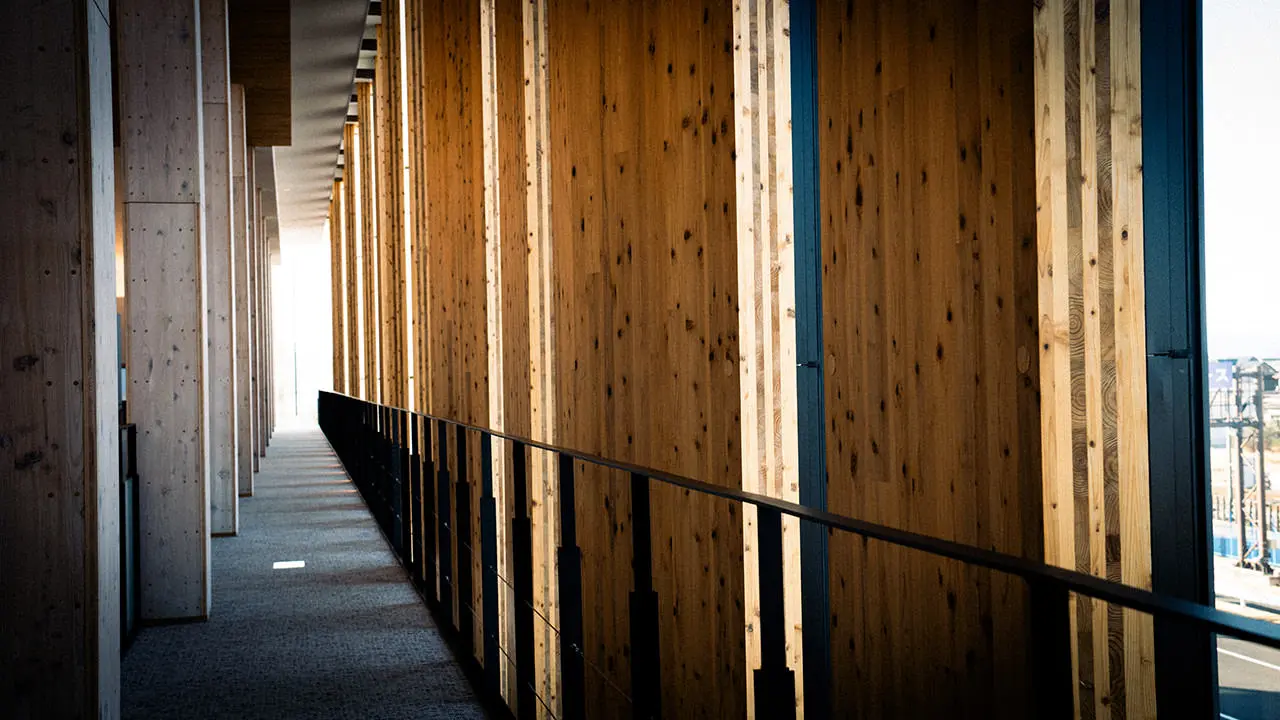
The north entrance hall surrounded by Chichibu cedars, OKI Honjo Plant's H1 Building is the flagship factory that implements the "Manufacturing DX" solution concept for realizing DX in the manufacturing industry. It received the Nikkenren Commendation 2024 65th BCS Award and the SAITAMA Social Contribution Award for its forest recycling activities at the former site where Chichibu cedars were logged (Minano Town, Chichibu County, Saitama Prefecture), which were used in the building.
https://www.oki.com/jp/press/2024/02/z23071.html
(TeleGraphic Editorial Board)
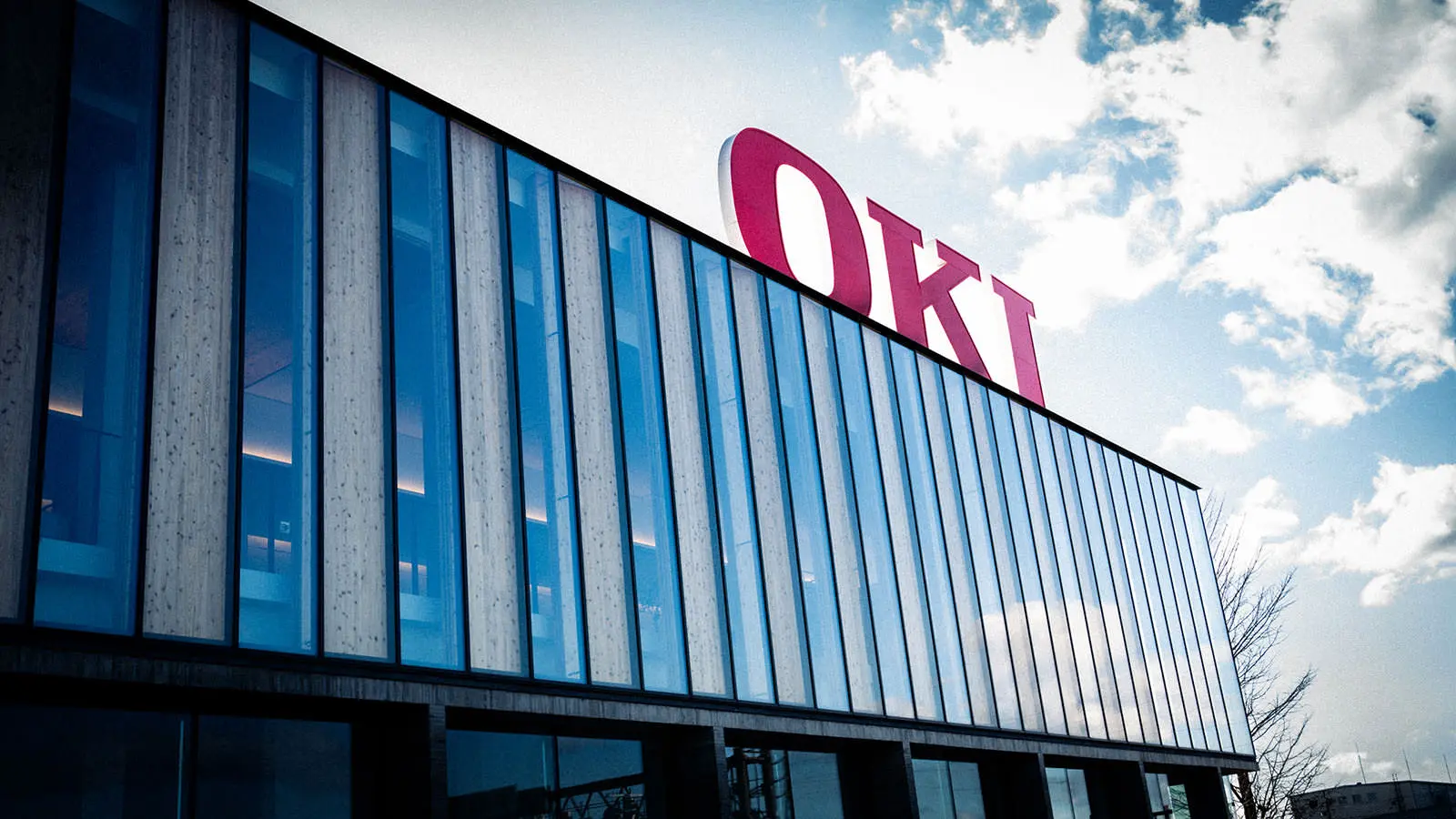